范小林博士
隧道窑砖瓦焙烧的原理
焙烧
砖坯在隧道窑中经过850~1050℃温度的烧结,并维持一定的时间间隔,在窑炉进行内热加工,完成一系列的高温物理化学反应,使产品冷却后具有一定的机械强度和物理化学性能,这个过程即为焙烧。
隧道窑焙烧的特点:
a、砖坯从进车端顶入,同时从出车端顶出;各车位温度固定(定带);最高温度车位固定(定点),最高烧结温度固定(定温)。顶车时温度向进车端移回一个车位;顶车后窑内的温度向出车端移动一个车位;当顶车的时间间隔等于温度回移一个车位的时间,最高车位位置和温度基本不变,火带温度基本不变,就实现了定带、定点、定温焙烧。
b、供风、抽烟和送热:隧道窑的供风从出砖端吸入或者鼓入,经过冷却带吸收砖余热加温后进入燃烧带,供氧燃烧,再经过高温预热带、低温预热带将烟气中的热量交换给砖坯,最后以余热约100℃左右烟气由抽烟风机抽出焙烧窑后再鼓入干燥窑作为烘砖的热源。送热风机从冷却段抽出加热后空气直接送干燥窑烘砖,此时鼓入窑内的风量需大于或者等于送热和抽烟风机从窑内抽走的风量。
发热量、热平衡与焙烧的温度,富氧和欠氧燃烧
燃烧应该满足3个条件:可燃物质、达到该物质的燃点、有足够的氧气。
在砖瓦窑炉焙烧过程的热平衡中,可燃物质是煤,采用空气供氧。空气中的氧含量为21%,79%为其他不助燃的气体。提供空气助燃时,一是煤燃烧发出热量;二是把砖烧熟消耗热量;三是抽出含有温度高于100℃的二氧化碳和79%的空气中氮气的烟气,从窑内带走热量;四是窑车出砖从窑内带走热量;五是窑体散热带走热量。
内掺或者外投煤燃烧发出热量为进入窑内的主要热量,按中华人民共和国《烧结砖瓦能耗等级定额》-JC/T713-2007人工干燥隧道窑烧成单位总热量定额为:
一级350大卡/公斤产品
二级385大卡/公斤产品
合格425大卡/公斤产品
以一个3.3米断面,100米长的隧道窑热平衡计算表为例:
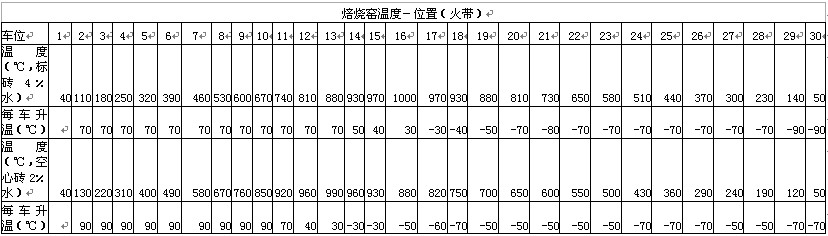
从表中可以看出:
A、当输入给焙烧窑的热量小于支出的热量时,温度达不到最高烧成温度所需的烧结最高温度;
B、坯体化学反应耗热仅17.70%,余热利用潜力大;
C、减少热量支出的主要措施在于利用自然干燥降低砖坯的水份,入窑砖坯水份降低3%,热量支出将减少10%;人工干燥比自然干燥多用27%的煤。
D、延长出车时间到1.5倍(即90分钟时),烧蹲火,热平衡计算表中5,6,7,8,9,10,11款增加热量支出25%.
E、当抽风量高于最佳的空气过剩系数时,如果抽风量大于50%,富氧燃烧,烟气带走热量支出增加10%,窑内温度能量下降10%;
F、当抽风量低于最佳的空气过剩系数时,为欠氧燃烧。若抽风量不足最佳空气过剩系数的50%时,为全部燃料产生一氧化碳的不完全燃烧,其发热量约为完全燃烧的30%.如果抽风量再减小10%,至少有20%燃料会发生一氧化碳燃烧,燃烧发热量转换成温度至少减少14%;窑内温度能量至少下降14%.
从热平衡例子可以看出:在焙烧的时候,若多10%的空气,只多支出热量2%;但若少10%的空气,则发出的热量将减少14%.
预热、烧结、冷却的温度--位置关系
1、定义
砖瓦焙烧窑位置温度关系定义为火带;
隧道窑温度--车位关系曲线定为火带曲线。
2、按焙烧基本功能定义火带
把从砖坯进窑后升温到850℃的车位带定义为预热带(分成低温、高温预热带)、把从升温到850℃,又升温到最高温度,再下降到850℃的车位带定义为烧成带、把从下降到850℃后又降温到出砖温度的车位定义为保温冷却带。
3、按煤的燃烧位置定义火带
把从砖坯进窑后升温到600℃的车位带定义为低温预热带;把从600℃升温到850℃的车位带定义为高温预热带;把从850℃升温到最高温度(约1000℃)的车位带定义为焙烧带;把从最高温度下降到850℃的车位带定义为保温带;把从下降到850℃后又降温到出砖的车位带定义为保温冷却带。
以下是一个30个车位的标准火带设计:
A、假定进焙烧窑的砖坯是含水份为4%的标砖,最高烧结温度车位在16车位,温度是1000℃,火行速度为每小时一车。从进车到850℃,每小时车升温70℃(70℃/小时),到达高温880~1000℃为3个车位,分别升温为50℃/小时,40℃/小时,30℃/小时;1000~880℃时降温分别为30℃/小时,40℃/小时,50℃/小时,其他点降温为70℃/小时。在2~4车位,温度升温超过70℃/小时,容易发生爆坯和网状裂纹;在22~25车位,温度降温超过70℃/小时,容易发生冷却发纹和哑音。最佳烧结点为1000℃,烧成温度范围为970~1030℃;过火报警温度1080℃;欠火报警温度920℃;火带的分布见下图所示:低温预热带1~9车位、高温预热带9~12车位、焙烧带13~16车位、保温带17~21.5车位、冷却带20~30车位。
B、假定进焙烧窑的的砖坯是含水份为2%的空心砖,最高烧成温度车位在13车位,温度是990℃,火行速度为45分钟一车。从进车到850℃,每车升温90℃(120℃/小时),到达高温850~1000℃为4个车位,分别升温每车70℃,40℃,30℃,为93℃/小时,53℃/小时,40℃/小时;1000~870℃时降温分别每车为50℃,60℃,70℃,每小时降温为66℃/小时,80℃/小时,93℃/小时,其他点降温为每车50~70℃。在2~3车位,温度升温超过150℃/小时(每车112℃),容易发生爆坯和网状裂纹;在21~23车位,温度降温超过93℃/小时(每车-70℃),容易发生冷却发纹和哑音。最佳烧结点为990℃,烧成温度范围为960~1020℃;过火报警温度1050℃;欠火报警温度920℃;火带的分布见下图所示:低温预热带1~9车位、高温预热带9~12车位、焙烧带13~16车位、保温带17~21.5车位、冷却带20~30车位。
上述的温度--位置曲线关系,用每车的顶车时间换算,得到温度--时间曲线关系,两者原理相同,表现方式不同,其中换算关系是火行速度(米/小时)。
砖瓦窑焙烧火行速度与产量关系
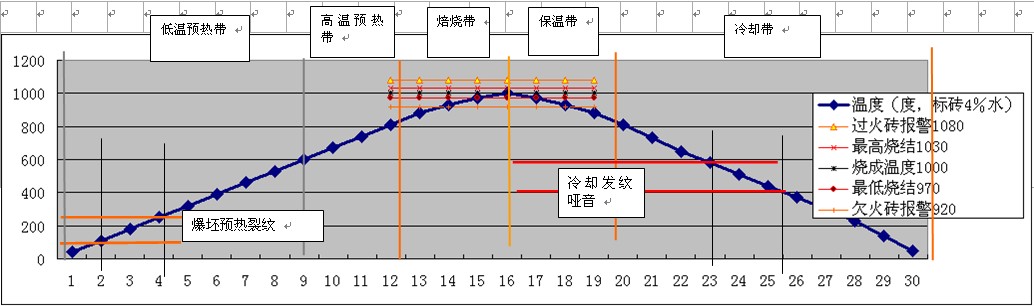
从焙烧过程总体来看,轮窑是火走砖不走,隧道窑是砖走火不走。从隧道窑在一车的顶车时间内来看,火仍然是从出车端向进车端行走,火行每走一个车位,隧道窑顶一车,将火顶回原位,顶车快慢与火速相等,维持火定点不走;轮窑火行每走一个窑门,移动风闸一个窑门,让风跟踪火行速度。
下图兰线为标准火带,红线为实际火带。5:50分顶车后,实际火带向出车端移动一个车位:
火行和风向
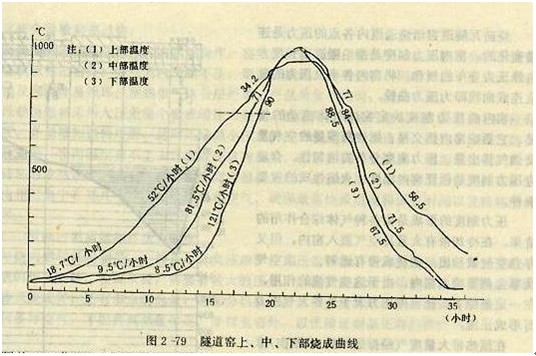
顶车后75分钟,实际火带向进车端移动一个车位4.35米,并与标准火带重合,可以顶下一车:
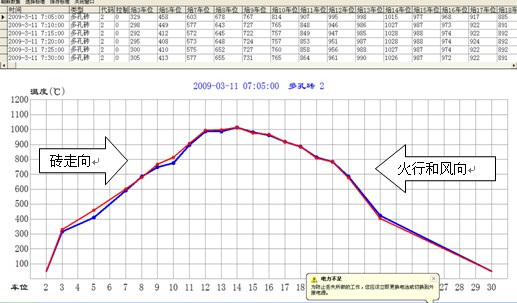
按上述的焙烧火行速度为75分钟一个车位:4.35米,火行速度为3.48米/小时。每车为KB1多孔砖5840块,折标9928块,每天产量19.2车,每天生产多孔砖112128块,折标190617块(6.9米大断面)。火速决定产量。
实现定温、定点、定带焙烧
定温:确定焙烧的最高温度;定点:确定最高温度点的车位;定带:确定一条温度标准火带曲线。
如果按标准火带曲线烧砖,当实际火带曲线(红线)与标准火带曲线(兰线)重合即顶车,就可实现定温定点的焙烧。
当火行没有达到标准兰线时提前顶车,火带向出砖方向后移;当火行达到标准兰线后顶车,火带向进砖方向前移;加快顶车,火带后移的办法为杀鸡取蛋的焙烧,此时产量是顶出的,而不是烧出的产量。烧蹲火不揭开火眼减速,仅仅延后顶车焙烧,火行速度将急剧加快,引起预热带温度偏高。如果湿坯进焙烧窑,还可能出现爆坯和因预热升温过急,水汽蒸发过急或者水份排出困难而产生的干燥裂纹。定点、定温、定带焙烧是隧道窑稳定高产、高质量、低煤耗最基本的焙烧方法。拉锯式(火带前移又后移)的烧法,将带来产量、质量、煤耗不稳定。
压力曲线:在进窑的风量和风压确定后,抽烟、和送热风机的风量与窑的阻力形成隧道窑中的各个车位的风压,其含义是间接测量鼓风风量、送热风量、抽烟风量,并使其风压平衡而达到风量基本平衡。大断面隧道窑的零压点一般在最高温度车位的前一个车位到后一个车位之间,当抽烟风机转速一定时,零压点越靠向进车端,风量越大;小断面隧道窑全窑负压,负压越大,风量越大,零压点在出车端。
以下是一个2.5米断面隧道窑实际测试的压力和顶部温度曲线:
16到23车位高温气体膨胀近3~4倍,流速加快3~4倍,该段两车位压差为17~25Pa,25~33车位压差为5~10Pa;15车位有漏风,温度下降了100℃,压力升高到30Pa;1~5车位哈风闸没有用起来,故最负的压力点在6车位。
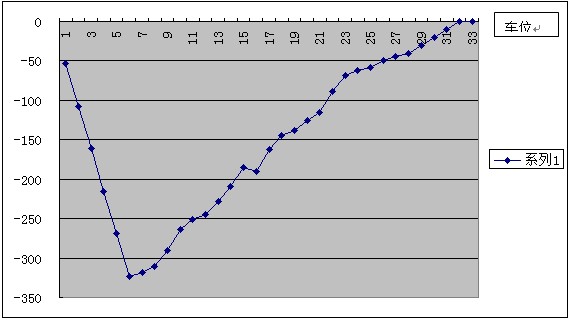
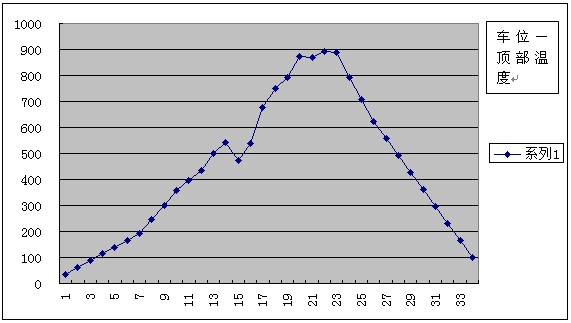
下面为一个大断面窑的压力曲线:
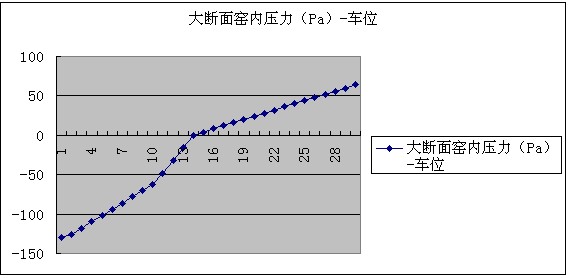
大断面窑对应的温度--位置曲线
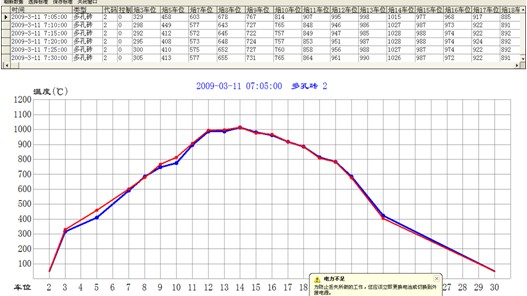
零压点在14车位,最高温度点在14车位;最高温度车位两车的压力差为4~5Pa/米,每车位压差17~25Pa(抽烟风);低温鼓风端为5~8Pa/车位(送热风+抽烟风)。
砖瓦窑焙烧火带、火速、层面温差关系
1、隧道窑的火带与层面温差关系
小断面隧道窑在高负压-320Pa下,抽风时插入顶部3cm的顶部风温,与插入顶部60cm的顶部风温的差距见下图:
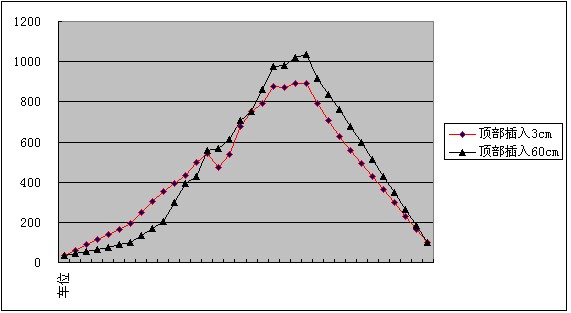
顶部负压和顶部风速度影响测温误差,当负压达到-320Pa时,风量大时顶部最高车位温度比中部温度约小100℃;在高温预热带,内掺煤开始燃烧,中部温度基本等于顶部温度;在低温预热带,中部温度低于顶部温度约100~150℃,其原因是车底的风从低温预热带传入窑内,和热烟气上升所致;在保温带和冷却带,顶部温度低于中部温度。
下图为大断面隧道窑上部、中部、下部的烧成时间--温度曲线:
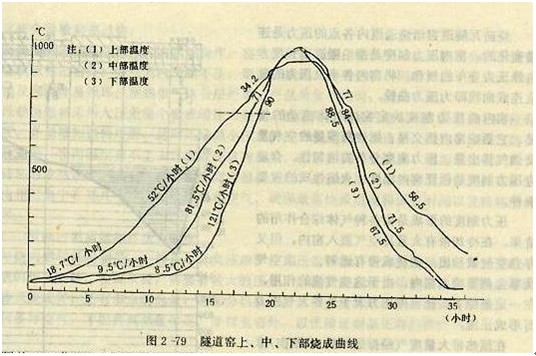
在高温、低温预热段由于中部和底部预热温度低于上部温度达到200~300℃,在高温预热段升温为上部52℃/小时,中部81.5℃/小时,下部121℃/小时;在焙烧段升温为上部34.2℃/小时,中部71℃/小时,下部90℃/小时;在保温段降温为上部-77℃/小时,中部-84℃/小时,下部-88.5℃/小时;在冷却段降温为上部-56.5℃/小时,中部-71.5℃/小时,下部-67.5℃/小时。最高温度点火行速度上、中、下都没有落后,中部和下部温度基本相等,上部温度比中下部温度约低85℃。
顶部测温误差还与顶部空隙大小有关,顶部间隙15cm与间隙35cm的温度检测误差达到60℃,间隙每增加10cm,经验数据是顶部检测温度降低30℃左右。
2、隧道窑风速风压与层面温差的关系及解决焙烧生砖问题
砖瓦焙烧时,一般会出现火跑面慢下底和火跑底不上面的2种错误焙烧方法。例如,上部在15车位达到最高950℃,下部在17车位达到最高950℃,这种现象是上部火行速度快于下部,俗称火跑面下底慢;反之,上部在17车位达到最高950℃,下部在15车位达到最高950℃,这种现象是上部火行速度慢于下部,俗称火跑底不上面;轮窑焙烧时采用先烧底,再反火烧面是正确的方法,但是隧道窑如果采用先烧底的方法,由于隧道窑无法调节放热闸烧反火,就会出现面上生砖。隧道窑最好的烧法是上中下火速齐头并进,不但产量高,而且煤耗也最低。
A、火炮面不下底,底部出欠火砖的原因及解决方案
火炮面不下底的原因如下:
(1)冷风从车底吸入或者灌入窑内造成的火炮面不下底
隧道窑与轮窑焙烧不同的是车底冷风,隧道窑的车底是一个进风口,进入多少冷风就会被窑内负压吸入多少冷风(不开平衡风机和平衡闸),这些冷风多从低温和高温预热带进入窑内,使预热带热风向上,导致预热带底部温度比上部温度低多达200~300℃,进入焙烧带后,底部温度落后于顶部温度,当落后达到3个车位以上时,底部出现生砖。解决的办法有:
① 沙封密封窑车侧边的进风口;
② 在从进车端起计算全窑的1/4处加一个车底隔风墙,在全窑的1/2处又加一个车底隔风墙,阻断负压段向窑内吸风;在保证车底温度低于90℃的前提下,可以在出车端加一个车底隔风墙。
③ 在全窑1/2处加一个车底隔断墙,进车和出车端各加一个车底隔断墙,调节预热段的车底闸、或者调节预热段抽风车底平衡风机转速和冷却段的车底平衡闸、或者调节冷却段鼓风车底平衡风机转速,使车底冷风不进窑内,同时窑内高温烟气不窜到车底(防止烧窑车)。
需要说明的是,直通式隧道窑因为排潮段负压最高,车底的冷风绝大多数都从排潮段进入窑内,不会因为车底冷风导致火跑面不下底,没有冷风导致底温低的现象。移动式隧道窑没有车底,从原理上讲没有这个问题。
(2)风量小,风速慢,底部缺风,导致火跑面不下底
假设由于窑车的原因,车面气体温度比上中部温度低50℃;热空气约以0.5米/秒速度上升,风量正常时横向风速为1.2~1.5米/秒,所以风在隧道窑是以20℃角向进车方向移动,车面供风基本均匀。
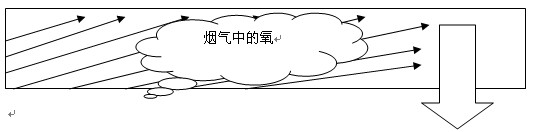
如果窑内供风不够,风量减小到30Hz以下的转速,风量减少一半,横向风速减小一半,上升速度不变,风向速度更向上,上升角度可达45℃以上。其结果造成窑车面温度比上部温度低,温差变大,燃烧也不如上部好,使下部温度更低,温差加大,形成恶性循环。热风飘上,底部供风不足,燃烧不好,层面温差加大,车面出欠火砖。所以“风大火下底,风小火跑面”就是这个道理。
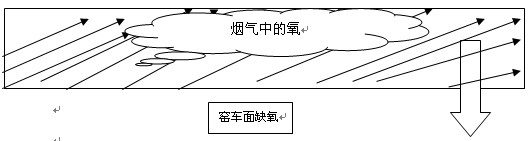
(3)“远闸火下底,近闸放底火”
在风量足够的情况下,哈风闸离最高温度的位置越远,预热带预热的时间越长,预热带上下温度均匀,火下底;哈风闸离最高温度的位置越近,底部抽热多,底部预热时间短,导致底部温度低,火不下底。
B、火跑底,窑面出欠火砖的原因及解决方案
火跑底是上部火行速度慢于下部火行速度,窑面出欠火砖的原理与火炮面的原理相同。如果顶部出欠火砖,车面不出欠火砖,原因是窑顶的风量过大,导致风带走的热量大,顶部温度下降。导致窑顶风量相对于窑底车面大的原因有:窑顶间隙大,上部砖稀;风机开得大或者哈风闸提得过高。对应解决的办法是:减小窑顶的间隙,码砖做到上密下稀;或者减小风量(调低风机转速或者放低哈风闸)。
如果底部出欠火砖,窑顶出欠火砖,中部还出过火砖,其解决办法是调整码坯方式,中下部变稀或者顶部变密(堵住顶部空洞),同时火带后移,使底部预热时间变长,同时需要把抽热闸关掉;抽热闸离最高车位过近,如果温度高,拉高抽热闸放火,也会出现中部出过火砖的情况。
如果整窑出欠火砖或者过火砖,温度低,烧成段顶部温度与底部温度基本相等,此时应该判断为内掺太低或者过高,需要增加内掺和外投煤或者减少内掺。
干燥窑温度标准曲线设计
烘干窑预热升温速度设计为5~7℃/小时,进入烘干窑砖坯的温度为25℃,需要烘干时间为8小时,约8~9个车位升温;恒温排潮温度为70~75℃,时间为8个小时,车位为9~16车位;快速烘干时间为4个小时,升温速度为10℃/小时,车位为17~20车位。设计烘干窑车位--温度曲线见下图所示:
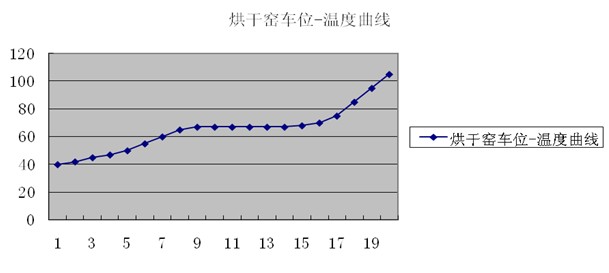
排潮口的温度为45℃,位置在2~5车位,夏天进窑砖坯温度为40℃,在2车位排潮;冬天进窑砖坯温度下降到5℃时,为保证排潮口温度仍然在45℃左右,排潮口需移动到窑内温度为45℃的5车位处,从夏天的2车位移动到冬天的5车位,多用3个车位来升温20℃以抵消气候下降的20℃。
自动焙烧系统温度控制功能
风量大小可控制燃烧程度,风既可以助燃,也可以灭火,其道理犹如水可浮舟,水也可沉舟,一定燃料下的最佳配风燃烧是温度的间接控制,温度的控制又是产量、质量、煤耗的间接控制。系统中多车位顶温和车面温度的控制是温度曲线或者温度场的控制,通过对标准曲线的优化,并稳定在标准曲线下焙烧,实现焙烧工艺的产量、质量、能耗的控制。
焙烧标准的建立方法和原则
A、建立焙烧标准方法
(1)系统提供自动建立焙烧标准的功能;
(2)人工修改标准:
① 整窑砖过火,降低最高温度5个车位的标准温度;
② 整窑砖欠火,增加最高温度5个车位的标准温度;
③ 降低标准温度,自动配风风量增加,火速加快,烧结时间将缩短;提高标准温度,风量将减少,火速放慢,烧结时间延长。
④ 当新换砖型进入最高温度车位时,选择该砖型对应的标准曲线进行焙烧。
B、标准的设定原则
最高温度在±10℃内微调;最高温度车位在±2个内调整。
自动判定合格砖的原则
(1)顶车打铃过快应调高标准;
(2)顶车打铃过慢应降低标准;
(3)设定顶车底部温度低限和层面温差高限;
(4)设定顶车顶部温度低限和控制误差判定限,当温差小于控制限时才顶车打铃。
自动配风控温设定参数
(1)设定烧成最高和最低温度;
(2)设定风量高限和低限;
(3)设定预热带和保温带允许的偏差;
(4)设定烧蹲火(吊火)的最低风机转速;
(5)大断面的风机比例联动调节系数;
(6)设定过火砖和欠火砖报警温度。
上述参数设定好后,自动配风在最高和最低烧成温度范围内会根据窑内供氧、内掺、温度带的情况,自动加风或减风。
自动喷煤(投煤)控温设定参数
(1)顶温喷煤温度:顶温低于该温度,喷煤或者提示投煤;
(2)底温喷煤温度:底温低于该温度,喷煤或者提示投煤
(3)喷煤时间:自动启动喷投煤机运行达到该时间间隔后,自动停止喷投煤;
(4)停止喷煤间隔:上次喷投煤完成后计时,计时达该间隔时,做第二次喷投煤温度比较和控制加煤。
车底风压平衡调节
给定平衡风压差后,计算机将自动调节平衡风机,使窑内风压和车底风压的差值在给定的范围内。